
This article appeared in the July/August issue of
Good Old Boat.
Anyone that owns or is considering the purchase of an older boat that is in need of some renovations has wrestled with what to do with worn or faded non-skid surfaces on the decks. There are several options including artificial materials glued to the decks, paints and coatings. Our Mariner 40 ketch,
Sea Trek, has just had the 30th anniversary of the laying of her keel. We lived aboard and cruised her extensively for 17 years and the

repairs and renovations were ongoing from the beginning. While she had not been abused, she had not been used and was allowed to simply sit at the dock uncared for. Simple cosmetics like redoing the extensive teak trim was easy although time consuming. Our plans were two fold; first to bring her back to like new condition, and second to make her as safe and comfortable as possible for offshore and coastal cruising.
After a few short term cruises on the Chesapeake Bay, we came to several conclusions. One that stood out was the fact that th

e non-skid was non-skid no longer. Also, the finish was badly faded and worn, despite the lack of use. So we began our research of just how we might do this without spending serious dollars or hiring a professional. One of our goals was to do any repairs or renovations ourselves to save money, to improve our skills and knowledge, and to know that the boat was done to our liking and expectations. Our first attempt was to try the easiest and most obvious. We decided to paint the surface close to the original non-skid color and not change the surface texture. This first try was done using Awlgrip paint for it toughness and ease of application. We used a flattening agent to

take the high gloss out so it would not be so slippery. This looked great but the reality was that underway with rain or seas breaking on the deck, we still had to crawl down the deck to go forward because you had a hard time keeping your footing. So it was time for plan B, and there is always a plan B.
With more research came several expensive and very labor intensive choices. If we went this route, the cruising would have to be delayed and we would have had to plan for a fair amount of our free time to complete the project. Almost by

accident, we came across a post on a cruisers web site about a product called Tuff Coat by Ultra Tuff Marine www.tuffcoat.net that could be painted on the deck, came in different colors and was touted as a true non-skid that would not break the bank. The manufacturer claims the product is used in industrial applications and is used by military and commercial shipping alike. It sounded like the answer to our dilemma and more web research brought very positive feedback. And also as important, it fit into the budget. While we waited for the product to arrive we studied the installation requirements and even began

preparations.
The first requirement was to thoroughly sand the surface to be covered with a 40- to 60-grit sand paper. Needless to say, this did a number on our painted surface and almost completely smoothed out the texture on the non-skid areas. We had to be very careful not to sand into the adjoining painted surfaces. Did I mention that we had completely Awlgripped the entire boat from the waterline to the masthead? Once the sanding was completed we cleaned all surfaces with soap and water and waited for the product to arrive.

For the square footage of our decks that needed to be covered we calculated three gallons and decided to order four. An epoxy primer recommended by the manufacturer was also needed so we ordered a gallon, plus the special roller applicators needed. The entire process was a bit more time consuming than we anticipated. As with any project like this the preparations are not only important but can take up the most time. The first step was to remove any deck hardware we were able to or felt that it would be more beneficial than leaving. There were some items such as handrails that would mean removal of interior headliners and such that we chose to
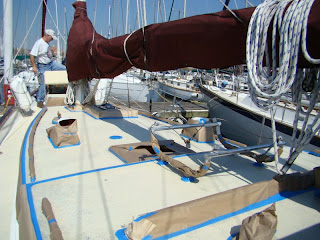
leave in place. Once the items were removed, the painted areas and whatever was left in place needed to be taped around securely. Rounded corners and odd shapes required a bit more effort, and then a strip of 9” paper was added to the taped strips to prevent splatter. Getting all of this in place took much longer than the actual painting of the coating.
Once all of the taping was finished, we laid on the first coat of primer. This was in two parts that need to be mixed in the correct proportions. Once mixed, it must be used, since it cannot be kept for

very long even in a closed container. We were able to mix enough to cover all of the decks on the first pass. A small paint tray and a 4-inch closed foam brush made applying the primer a quick and easy task. The primer is little more that the consistency of milk and only a light coat was needed. There is no need to sand the primed surface prior to the top coat. Once done, a 24 hour wait is required before the coating can be applied.
The final finish needs to be done in two coats. There is a special foam roller that is used for the

application to give the surface a uniformed textured look and an ordinary brush to “dab” the topcoat in areas that the roller won’t reach. The coating has suspended particles that require thorough mixing throughout the process. We use a mixer attached to an electric drill to get a good mix in the can. The first coat is laid down in strips of about 3 feet rolled on alongside each other but not overlapping. Complete coverage is not important at this point but keeping the roller moving in the same direction is. Once an area of about nine square feet is covered, the coating needs to be rolled at a 90-degree angle to the first application and worked in until there is a pretty

uniform coverage. Total cover is still not important yet, but a uniform texture is. In a short period of time, you get the technique down easily. This whole process is continued till the entire non-skid areas are covered.
Once the first coat is dry to the touch, the second coat needs to be applied. It is important that this be done quickly and not left until the next day. For us, once we were finished with the first coat it was dry enough for the second. The process is the same as the first coat, except that attention should be paid to getting complete coverage with this coat. To cover
Sea Trek’s decks with two

coats took us a total of three hours. Once the second coat is completed, the paper and tape must be removed immediately. Leaving the tape too long can pull the coating off of the edges when the tape is removed. As soon as the second coat was completed, we pulled first the paper then the tape around the edges. This can be a bit acrobatic while trying not to walk or lean on the coated areas. Once all of the tape and paper was removed, we had to just stay off the decks for several hours. After that, we were able to walk carefully on the surface in stocking or bare feet. Ideally we wanted to stay off for 48 hours to give it plenty of time to dry. The final step is to

re-install and re-bed the hardware that had been removed. Any time hardware is removed and re-installed on the decks, we soak the holes for the fasteners with thinned epoxy to completely seal the deck core so it can not leak or absorb water if the bedding fails.
One of the big challenges in this project is not letting the decks get wet for 48 hours. Careful planning for weather, keeping your dock neighbor from hosing it down and other considerations come into play. One of our concerns was evening dew settling on the surface. We waited until there was no rain in the forecast and the relative

humidity was projected to be low. This can be difficult with a boat sitting in the water. Perhaps done on the hard or in a shed with a controlled environment would be the best way to go. As it turned out we had no problems. The finished result looked fantastic and was better than we expected. Taking our time during the application process we were able to get a good looking uniformed texture that rivaled or bettered many factory finishes on the dock. But best is the entire surface was indeed a true non-skid which did not seem to be affected by water or the kind of footwear, or lack thereof, you might be wearing. It appears to be rugged and has held up to

anchoring, piling chain up on the foredeck and whatever else we have done in the normal process of sailing the boat. Our entire time invested to completion was about three days. How long the finish will hold up and how long it will continue to look great…only time will tell. But for now we are very optimistic and would recommend anyone contemplating the refinishing of their non-skids to consider this option.