Unfortunately, work has seriously interfered with the boat projects and this winter saw very few of the items on my to-do list get done. One project that we did start before the blizzards set in was to redo the shower in the forward head. We had converted the head into a shower when we first moved on the boat, but it was a temporary fix and we planned on a more permanent finish later. Later began in December after the boat was hauled and we moved ashore. I began taking the old Formica like material off of the walls and planned to replace it with
FRP panels that would look better, be completely waterproof and easy to clean. These are the typical panels found inside many shower enclosures.

First we had to remove the mirror, towel bars, soap dishes, teak racks, and whatever items were attached to the walls, and remove the sink, which slides out from behind the head and has a diverter in the faucet for the shower hose. The plumbing lines to the sink had to be capped off so we could use the fresh water system until the project was completed. Then the original wall covering could be removed. The old material was actually quite easy to remove with a heat gun and a wide scraper. With a few passes of the heat gun and the scraper behind the panel, as soon as the old adhesive warmed up a bit, the panel pulled loose. It was a bit tedious but the panels came off in large pieces with minimum effort and since the old adhesive that held them up was pretty thin, there was only a little sanding

needed to get the plywood behind it ready for the new panels. Once the old panels were off and the plywood sanded, we used a
two part penetrating epoxy to further seal the walls against water intrusion. The under-layer of plywood was in excellent condition and there were no signs of water leaking into it at any point. This was probably because none of the past owners had ever installed a shower on the boat in either head. With the walls now sealed, it was time for the next step.

Since there are no square corners on a boat, simply measuring an area and cutting the panels to fit would not quite work for us. So it was necessary to make templates for the three areas we would be covering with the panels. We needed something that would allow us to work in the small space and still be rigid enough to maintain its shape and size when we transferred the shape to the FRP panels. After a little thought and a walk through the local hardware store, we settled on using
underlayment for Laminate Flooring. It is very inexpensive, comes in 48-inch rolls and has just the rigidity needed. By cutting sections just slightly larger than the area for which we needed to make the template, the material was taped to the longest straight run on the wall. Then, the material was marked off with a felt pen and cut to size with a pair of scissors. Once cut to size, the templates were placed back on the walls to be sure the fit was right.
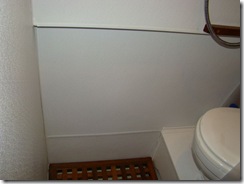
Next the templates were transferred over to the panels, placing them in reverse on the back of the panels and marking them with a felt marker. The panels were cut with our Ryobi battery operated circular saw and a saber saw, both with fine blades for cutting plastic. The circular saw made all of the straight cuts and the saber saw did all of the irregular cuts. Once the panel was cut it was held up on the wall and dry fitted. They usually needed a little adjustment depending on how complicated the pattern was. We had also purchased the inside and outside corner moldings for the panels so they were also cut to size. Placement of the moldings need to be considered, since they fit behind the panels, you have to determine when the molding needs to go on in relation to the panel already up and the next one to go up. Once all of the pieces of the puzzle were cut and their fit confirmed, it was time to attach them to the wall. There are a few options to glue the FRP panels to the walls, and we chose the
Liquid Nails specifically for these panels.

The Liquid Nails adhesive was removed from the can and smeared on the plywood with a putty knife and then spread out over the area with a notched trowel like those used to apply adhesive for ceramic wall tile. The notches apply just the right amount of adhesive as long as the entire surface is covered, being careful to not leave any bare spots. The adhesive requires that the material be set into it within 45 minutes or before the adhesive begins to skin over. With this in mind, we did each of the three sections, one at a time. In addition to the adhesive, all corners were thoroughly caulked with 3M 4200 to insure water would not leak into the corners. With good coverage with the adhesive and the panels in place, it

was necessary to place braces made from 1”x 2” strips between the panels and the opposite wall, to hold the panels tight into the adhesive until it had time to dry. This was due to the rigidity of the panels and the tendency to pull away where the walls or panels were bowed.

With all of the panels in place, the shower was beginning to take shape. The bottom edges where the panels meet the shower pan would need to be sealed completely. This is usually the area that will leak first if that were going to happen. For this, we used a vinyl strip that could be folded and would cover both the bottom of the panel and the lip around the pan. The corners have also been caulked thoroughly with 3M 4200 to seal everything and keep it that way. Next, the moldings where the panels meet the ceiling had to be installed. With the corner moldings in place and allowed to dry thoroughly for a day or two, we could begin the process of reinstalling everything back in place for the towels and various sundry items we use in the shower. Instead of just reinstalling everything back where it was, we planned where everything would go to keep the things that needed to stay dry in certain areas and also placing anything that would protrude from the walls in areas that would not cut down on space when we shower.

All items attached to walls where sealed with caulking so that even the screw holes could not leak. We added a
shower curtain slide system on the ceiling that would allow the shower curtain to slide easily but would keep it close to the walls. This gave us maximum space with the shower curtain in place and left a feeling of openness to the shower. Towel rings, teak racks, the mirror and a shower caddy for soap, shampoo, wash cloths, etc. all went in strategic locations. Everything worked out just as we planned and the shower turned out to be all we had hoped for. While we had the sink removed, we used to opportunity to paint areas that were hard to get to, like the inside of the hull behind the

sink. We also painted the area under the head where the new thru-hull had been installed before we launched. Once the project was completed and we had our first shower of the season on board, we were very pleased with our modifications. And the entire shower proved to be very water tight as we had hoped. Now for the next project.